For an air abrasive blasting system to work effectively, you must have good equipment, quality control of the operation, and a trained operator using proper blasting techniques. This column will briefly review equipment and quality control requirements, which were covered in the November 1998 Applicator Training Bulletin (“Setting Up Abrasive Blast Equipment for Steel,” pp. 46-49), and then it will offer some advice about blasting techniques. In addition, solutions to problems of moisture in the system that arise from working in humid environments will be presented.
Equipment and Quality Requirements
To achieve high quality cleaning at an acceptable production rate, you must use the proper combination of equipment and make appropriate quality control checks, including the following.
- Compressor—The compressor must be big enough to deliver sufficient air volume and pressure for maximum productivity. Factors affecting compressor size requirements include the number and length of blasting hoses to be used as well as the nozzle orifice size and the air hose and coupling size. The compressor size is chosen on the basis of the required air volume (i.e., cubic feet or cubic metres per minute) and air pressure (i.e., pounds per square inch [psi] or bar). In addition, the amount of breathing air needed and compressed air requirements for other equipment, such as after-coolers, etc., must also be considered.
- Blast machine—The blast machine is a coded pressure vessel with appropriate piping, valves, and fittings. It must be manufactured and used in compliance with European Union directives and national regulations, which vary depending on where the work is being done. The blast machine should have a metering valve for precise adjustments of abrasive flow and a remote-control switch on the nozzle for the blaster to shut down the system whenever necessary.
- Hoses and fittings—Air hoses, blast hoses, and release couplings must be sized appropriately so they do not have a negative effect on blast pressure at the nozzle. Conditions that increase friction and impede air or abrasive flow (e.g., restrictive fittings, small diameter hoses, excessive hose length, or small radius bends in the hose) should be avoided. Pressure at the nozzle, as measured by a needle gauge, should normally be in the range of 6-7 bar.
- Nozzle—The blast nozzle orifice size must be appropriate for the work. The nozzle interior must not be worn excessively. An increase of more than one nozzle size (~1.5 mm) is excessive. The nozzle length should suit the blasting job. Normally, short nozzles (~7.5 cm) are used for easy-to-clean surfaces, and long nozzles (11.5-22 cm) are used to remove tenacious materials. Special nozzle configurations are available for cleaning hard-to-reach surfaces such as pipe interiors.
- Quality control checks—Oil and moisture in the air supply can be eliminated by an oil and moisture separator on the air line. A blotter test can be used to check for air line contaminants. The abrasive should be tested for size, dryness, and the possible presence of contaminants before it is used.
- Abrasive setting—Productive blasting requires the use of just the right amount of abrasive. Too much or too little abrasive lowers productivity. Abrasive adjustment is made with the metering valve. There is no scientific way to determine the setting. Adjust the valve until you hear the blast line “sing.” More is not necessarily better. Feeding in more abrasive not only can lower productivity but it also can cause an unsightly cloud of dust and visibility problems.
Blasting Techniques
Presuming that you have an efficient combination of equipment and dry abrasives and that you are using them according to manufacturers’ directions, then the final requirement for a productive system is effective operation by the blaster. There are three main elements of technique in abrasive blast cleaning: stand-off distance, angle of deflection, and dwell time.
Stand-Off Distance
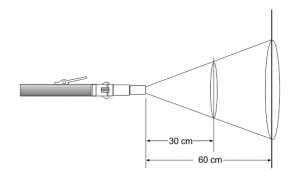
Stand-off distance is the distance from the blast nozzle to the workpiece. The shorter the stand-off distance, the more cleaning power the system has, but the smaller the blast pattern becomes (Fig. 1). Thus, there is a trade-off between cleaning power and productivity in the selection of stand-off distance.
When tenacious materials such as mill scale must be removed, it is likely that the stand-off distance will have to be relatively small, in the range of 30 cm. The stand-off distance can be increased to about 60 cm when less tenacious materials such as old paint are being removed.
When you first begin blasting, you should experiment with stand-off distance until you determine the optimum distance for cleaning and, at the same time, for achieving the greatest production speed.
Angle of Deflection
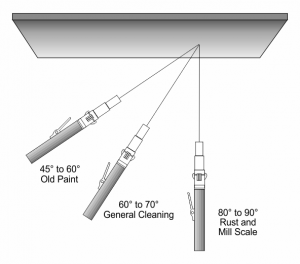
It is also necessary to determine the optimum angle of deflection—the angle of the nozzle in relation to the work-piece—when you first begin blasting (Fig. 2). For rust, mill scale, and heavily pitted surfaces, the angle of deflection should be 80-90 degrees. For removal of old paint, the angle might be about 45-60 degrees, and for general cleaning it can be 60-70 degrees.
A slight downward angle will help you direct the dust away from you as you blast so you can see the work better. In confined spaces, lighting may be required to help you see the work surface.
You must operate the nozzle consistently both as to stand-off distance and angle of deflection. In both vertical and horizontal movements, you must keep the nozzle parallel to the workpiece and avoid arcing movements that will move the nozzle further away from the surface at the end of the pass. At the same time, the optimum angle of deflection should be maintained.
To accomplish this consistency, you should limit the distance the nozzle travels during each pass across the work-piece. A good average distance for a pass is about 75 cm.
The consistent operation of the nozzle is similar to the consistent operation required for spray painting, where smooth, easy strokes are made across the surface, with one stroke partially overlapping another.
Dwell Time
Dwell time is the amount of time spent cleaning any particular spot on a workpiece. When loosely adherent materials are being removed, dwell time will be momentary on any given spot. When tightly adherent materials are removed, dwell time will be longer, perhaps as long as several seconds. Therefore, the travel speed of the nozzle will not be uniform, because it will be necessary to dwell more on some areas than on others.
When you are blasting irregular surfaces or when surface conditions are variable, it may be necessary to vary the stand-off distance and angle of deflection as well as the dwell time.
Dealing with Moisture Problems
One of the biggest problems with abrasive blasting is related to moisture. A large amount of abrasive blasting is performed during warm months when relative humidity tends to be high. Compressing air at moderate to high relative humidity results in air leaving the compressor holding a large amount of water vapor. However, when the temperature of the compressed air drops, some of this moisture may condense and form water droplets, which can dampen the abrasive and cause it to clog the blast system. In addition, damp abrasive blasted against steel substrates can promote flash rusting.
The most effective method of dealing with excess moisture is to use properly sized and operating moisture traps to remove any condensate. The valve on the bottom of the trap should be slightly cracked open. This allows the water to drain from the trap so it doesn’t fill and then add water to the air stream. Under certain conditions, an after-cooler may be necessary to cool the air. The benefit of this is that cool air holds less moisture than warm air.